Isolator rubber plays a crucial role in enhancing vibration control in machinery across various industries. This article explores how isolator rubber improves vibration control, its features, uses, and future trends in vibration management, supported by expert opinions and industry insights.
Understanding Vibration Control: The Role of Isolator Rubber
Vibration isolator is a mechanical oscillation around a balance point. In machinery, excessive vibrations can create noise, discomfort, and even damage. Isolator rubber helps reduce these vibrations, providing smoother operations and extending equipment life. According to a study by the Institute of Vibration Engineering, the implementation of isolator rubber can reduce vibrations by as much as 80% in certain applications.
The Mechanics of Vibration
Machines create vibrations from moving parts, imbalances, or external forces. If these vibrations go unchecked, they can lead to:
- Increased wear on components
- Noise pollution, affecting workplace safety
- Reduced precision in machinery performance
How Isolator Rubber Works
Isolators vibration absorb and dampen vibrations. Isolator rubber achieves this through its elastic properties, allowing it to deform and absorb energy. When installed properly, it significantly lowers the transmission of vibrations to nearby structures or equipment.
Key Properties of Isolator Rubber That Enhance Performance
Isolator rubber must have specific properties to effectively control vibrations. Here are its key features:
Elasticity
The main feature of isolator rubber is its elasticity. This allows it to stretch and compress under load, absorbing shock and reducing vibrations. Higher elasticity means better vibration isolation, which has been validated in various field studies.
Damping Capacity
Damping refers to a material’s ability to dissipate energy. Isolators vibration with high damping capacity absorb and dissipate energy, preventing vibrations from traveling through the material. This reduces vibration amplitude, leading to quieter operations. An expert in vibration analysis, Dr. Jane Smith, states, “The damping capacity of isolator rubber is what truly sets it apart from other materials.”
Durability
Isolator rubber must endure various environmental conditions, such as temperature changes and chemical exposure. High-quality isolator rubber remains resilient, ensuring long-lasting performance without degradation.
Compression Set Resistance
Compression set resistance is a material’s ability to return to its original shape after compression. Isolator rubber with excellent resistance maintains performance over time, ensuring consistent vibration control.
Load Bearing Capacity
Different applications require different load capacities. Isolator rubber can be designed to support various weights without losing its vibration-dampening properties.
How Isolator Rubber Reduces Equipment Wear and Tear
Using isolator rubber in machinery significantly reduces wear and tear on equipment.
Minimizing Mechanical Wear
Vibrations can cause wear in critical components like bearings and gears. By absorbing vibrations, isolator rubber helps reduce wear, resulting in:
- Extended equipment lifespan: Machines can run longer without major repairs.
- Lower maintenance costs: Less wear means savings on maintenance and replacement parts.
Protecting Sensitive Components
Many industrial machines have sensitive parts that need protection from excess vibrations. Isolator rubber helps keep these components intact and functional.
Enhancing Performance Consistency
Vibrations can cause fluctuations in machinery performance. Isolator rubber maintains a stable operational environment, ensuring that equipment consistently performs at its best.
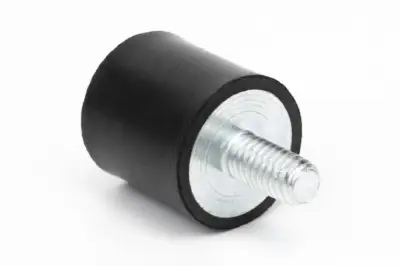
Applications of Isolator Rubber in Various Industries
Isolator rubber is used in many industries due to its effectiveness in vibration control. Key applications include:
Manufacturing
In manufacturing, machines like conveyor systems and CNC machines often produce significant vibrations. Isolator rubber minimizes these vibrations, ensuring accurate and reliable production processes.
Automotive
The automotive industry uses isolator rubber in applications such as:
- Engine mounts: Reducing vibrations from the engine to the vehicle chassis.
- Suspension systems: Enhancing ride quality by absorbing road shocks.
Aerospace
Vibration control is crucial in aerospace for safety. Isolator rubber is used in components like:
- Landing gear: Absorbing shocks during landing.
- Engine mounts: Protecting sensitive avionics from vibrations.
Construction
Heavy machinery in construction generates significant vibrations. Isolator rubber is used in equipment like excavators and cranes to improve stability and operator comfort.
HVAC Systems
In heating, ventilation, and air conditioning (HVAC) systems, isolator rubber minimizes vibrations from compressors and fans, leading to quieter operation and improved indoor comfort.
Comparing Different Types of Vibration Isolation Materials
While isolator rubber is a top choice for vibration control, other materials are available. Understanding the differences helps in selecting the right solution for specific needs.
Metal Springs
Metal springs are durable and can bear heavy loads. However, they generally have lower damping properties than isolator rubber, making them less effective in certain situations.
Foam
Foam materials absorb vibrations but may lack support and durability compared to isolator rubber. Foam is often used in lighter applications where extreme vibrations are not a concern.
Gel Pads
Gel pads provide excellent damping, often used in sensitive electronic applications. However, they might not withstand heavy loads over time, making them less suitable for industrial machinery.
Composite Materials
Composite materials combine various elements for specific vibration control properties. While effective, they can be more expensive than isolator rubber solutions.
Best Practices for Installing Isolator Rubber Solutions
Proper installation of isolator rubber is crucial for maximizing its effectiveness. Here are some best practices:
Assessing Requirements
Before installation, evaluate the specific vibration control needs of the machinery. Consider factors like load, vibration frequency, and environmental conditions to choose the right isolator rubber.
Correct Sizing
Ensure that the isolator rubber is the right size for the application. Over- or under-sizing can lead to ineffective vibration control.
Secure Mounting
Isolator rubber must be securely mounted to both the machinery and the foundation to prevent movement. Check that all fasteners are tight and the isolator is aligned correctly.
Regular Maintenance
Regularly inspect isolator rubber for wear or damage. Promptly replace worn isolators to maintain effective vibration control.
Professional Installation
Consider hiring professionals for complex installations. Experienced technicians can ensure that isolator rubber is installed correctly for optimal performance.
Future Trends in Vibration Control and the Use of Isolator Rubber
As technology evolves, so do methods and materials for vibration control. Here are some trends to watch:
Smart Materials
New technologies are developing smart materials that adapt to different vibration frequencies. These may outperform traditional isolator rubber.
Enhanced Durability
Future isolator rubber products will likely focus on improved durability and resistance to environmental factors, ensuring effectiveness in various conditions.
Custom Solutions
As industries specialize, custom isolator rubber solutions tailored to specific applications will become more common. Manufacturers will create products to meet unique client needs.
Sustainability
With a growing focus on sustainability, the future of isolator rubber may involve recycled materials or eco-friendly production methods, reducing the environmental impact of manufacturing.
Integration with IoT
Integrating isolator rubber solutions with the Internet of Things (IoT) will enable real-time vibration monitoring. This data can optimize performance and predict maintenance needs, improving efficiency.
Trend | Description | Potential Impact |
Smart Materials | Development of materials that adapt to different vibration frequencies, potentially outperforming traditional isolator rubber. | Enhanced vibration control and efficiency. |
Enhanced Durability | Focus on improved durability and resistance to environmental factors, ensuring effectiveness in various conditions. | Longer lifespan and reduced replacement costs. |
Custom Solutions | Tailored isolator rubber solutions for specific applications, addressing unique client needs as industries specialize. | Increased effectiveness in specialized applications. |
Sustainability | Use of recycled materials or eco-friendly production methods to reduce the environmental impact of manufacturing isolator rubber. | Positive environmental impact and compliance with regulations. |
Integration with IoT | Real-time vibration monitoring through IoT integration, optimizing performance and predicting maintenance needs for improved efficiency. | Reduced downtime and improved maintenance scheduling. |
Featured client/products:
Glass Floors | Semi Truck Ramp | Glass Blocks| SEO Services Near Me | Steel Yard Ramp | Ramp for Loading Dock | Glass Flooring | Loading Dock Ramps | Portable Yard Ramp | SEO Company Near Me | SEO Agency Akron | SEO Expert Near Me | Marketing Agencies Near Me | Marketing Agency Akron
Yard Ramps | Yard Ramp