Are you looking for reliable Clemco sandblasting equipment for your surface preparation needs? Sandblasting is crucial in many industries, from construction to automotive restoration. Clemco blasting equipment is known for its durability, efficiency, and versatility. This guide covers everything you need to know about Clemco blasting equipment, including its components, selection, safety precautions, setup, operation, maintenance, troubleshooting, and real-world applications.
Understanding Clemco Sandblasting Equipment: An Overview
Clemco Industries manufactures high-quality sandblasting equipment designed for surface preparation. Sandblasting, or abrasive blasting, propels abrasive materials at high speeds to clean or etch surfaces. Clemco sand blasters effectively remove paint, rust, and other contaminants.
The Importance of Sandblasting
Sandblasting serves several essential functions:
- Surface Preparation: Cleans surfaces for painting or coating.
- Restoration: Restores old and damaged surfaces to a new appearance.
- Versatility: Works on various materials, including metal, wood, and concrete.
Clemco blasting equipment efficiently handles these tasks, making it a preferred choice for professionals. According to a study by OSHA, proper surface preparation is critical for ensuring the safety and durability of coatings in industrial applications.
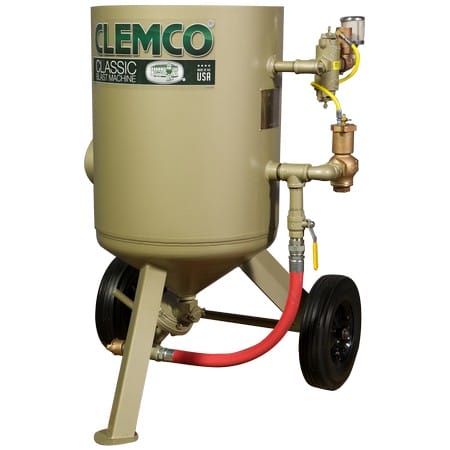
Key Components of Clemco Sandblasting Systems
Understanding the key components of Clemco sandblasting systems ensures effective operation. Each part plays a vital role in the efficiency and safety of the sandblasting process.
Blast Pots
The blast pot is the heart of any Clemco sandblaster. It holds the abrasive material and regulates its flow during blasting. Key features include:
- Pressure Regulation: Maintains consistent pressure for optimal blasting.
- Capacity: Available in various sizes for different project needs.
Nozzles
Nozzles direct the abrasive material toward the surface. Clemco offers various nozzles with different diameters and styles for diverse applications.
- Venturi Nozzles: Provide increased abrasive velocity for high-efficiency blasting.
- Straight Nozzles: Suitable for general-purpose blasting.
Air Supply System
A reliable air supply system is crucial for Clemco sandblasters. This includes:
- Compressor: Supplies air pressure for the system.
- Hoses: High-pressure hoses connect the compressor to the blast pot and nozzle.
Abrasive Material
Clemco sandblasters can use various abrasive materials, such as sand, glass beads, and aluminum oxide. The type of abrasive impacts the finish of the blasted surface.
Safety Equipment
Safety is a top priority in sandblasting. Clemco offers various safety equipment, including:
- Respirators: Protect against inhaling harmful dust.
- Protective Gear: Shields operators from flying debris.
Selecting the Right Clemco Model for Your Project
Choosing the right Clemco sand blaster model for your project is vital for achieving optimal results. Various models cater to different needs.
Factors to Consider
- Project Size: Larger projects may need bigger blast pots with higher capacities.
- Type of Abrasive: Different models work best with specific abrasives.
- Surface Type: Consider whether you will be blasting metal, wood, or concrete.
Popular Clemco Models
Clemco offers several models, including:
- Clemco Classic Blast Pot: A versatile option for most applications.
- Clemco Supa Blast Pot: Designed for high production rates.
- Clemco Mini Blast Pot: Ideal for small projects and tight spaces.
Safety Precautions When Using Clemco Sandblasting Equipment
Safety should always be your top priority when operating Clemco blasting equipment. Sandblasting involves high-pressure systems and abrasive materials that can pose risks if not handled correctly.
Essential Safety Measures
- Personal Protective Equipment (PPE): Always wear appropriate PPE, such as goggles, gloves, and respirators.
- Ventilation: Ensure the workspace is well-ventilated to prevent dust buildup.
- Training: Operators should be trained in the proper use of sandblasting equipment and safety protocols.
Risks of Neglecting Safety Protocols
Neglecting safety protocols can lead to serious injuries, including respiratory issues from inhaling fine dust, injuries from flying debris, and long-term health problems. According to the National Institute for Occupational Safety and Health (NIOSH), exposure to silica dust can cause silicosis, a lung disease caused by inhaling fine silica dust.
Emergency Procedures
Have emergency procedures in place, such as:
- First Aid Kits: Available on-site for immediate injury response.
- Emergency Shut-off: Accessible switches to stop equipment quickly in case of malfunction.
Step-by-Step Guide to Setting Up Your Clemco System
Setting up your Clemco sandblasting equipment correctly is vital for efficient operation. Follow these steps for a smooth setup.
Preparation
Gather all necessary equipment and tools, such as:
- Blast pot
- Air compressor
- Abrasive material
- Safety gear
Assemble the Equipment
- Connect the Air Supply: Attach the air compressor to the blast pot with high-pressure hoses.
- Install the Nozzle: Connect the appropriate nozzle to the hose securely.
Fill the Blast Pot
- Open the blast pot and add the chosen abrasive material.
- Close the pot securely to prevent spillage.
Conduct Initial Checks
Before starting the equipment:
- Check for leaks in the air hoses.
- Ensure all connections are tight.
Test Run
- Conduct a test run to ensure everything functions correctly.
- Adjust pressure settings for optimal performance.
Best Practices for Operating Clemco Sandblasters Efficiently
To maximize the efficiency of your Clemco sand blaster, consider these best practices:
Maintain Proper Pressure
Keep the correct pressure for effective blasting. Follow the manufacturer’s recommendations for optimal settings.
Use the Right Abrasive Material
Choose an abrasive material that suits your project. Using the wrong abrasive can lead to poor results or damage.
Practice Efficient Techniques
- Distance from Surface: Maintain a consistent distance from the surface for even coverage.
- Angle of Attack: Adjust the nozzle angle for optimal abrasive distribution.
Monitor Equipment Performance
Regularly check your Clemco equipment’s performance during operation. Look for signs of wear or malfunction and address issues promptly.
Maintenance Tips to Extend the Life of Your Clemco Equipment
Regular maintenance is essential for ensuring the longevity and performance of your Clemco sandblasting equipment. Follow these tips to keep your system in top condition.
Routine Inspections
Conduct routine inspections of all components, including:
- Blast pot
- Hoses and fittings
- Nozzles
Clean the Equipment
After each use, clean the equipment thoroughly to remove any leftover abrasive material. This prevents clogs and wear.
Replace Worn Parts
Regularly check for wear in critical components, such as nozzles and hoses, and replace them as needed.
Lubricate Moving Parts
Lubricate moving parts regularly for smooth operation and to prevent rust.
Common Issues with Sandblasting and How to Troubleshoot Them
Even with the best equipment, issues can arise during sandblasting. Here are common problems with Clemco sandblasters and troubleshooting tips.
Inconsistent Abrasive Flow
If you notice an inconsistent flow of abrasive material, check for:
- Clogs: Inspect hoses and nozzles for blockages.
- Pressure Settings: Ensure the pressure is set correctly.
Poor Surface Finish
A poor surface finish can result from several factors, including:
- Incorrect Abrasive Material: Ensure the abrasive suits the surface type.
- Nozzle Distance: Maintain the correct distance from the surface.
Equipment Malfunctions
If the equipment is not functioning correctly:
- Inspect Connections: Check all air and abrasive connections for leaks or loose fittings.
- Consult the Manual: Refer to the Clemco user manual for troubleshooting specific issues.
Comparing Clemco Sandblasting Equipment with Other Brands
When selecting sandblasting equipment, comparing Clemco sandblasters with those from other brands helps you understand unique features and benefits.
Advantages of Clemco Equipment
- Durability: Clemco sandblasters are robust, suitable for heavy-duty use.
- Efficiency: Features designed for performance often outperform competitors in speed and effectiveness.
- Versatility: Clemco offers a wide range of models and accessories, allowing customization for specific applications.
Competitor Comparison
While other brands may offer competitive products, they often fall short in:
- Customer Support: Clemco is known for excellent customer service.
- Availability of Parts: Replacement parts are widely available for Clemco equipment, ensuring minimal downtime. A case study from a large automotive restoration shop noted that they experienced fewer downtime issues with Clemco compared to other brands.
Real-World Applications of Clemco Sandblasting in Industry
Clemco sandblasting equipment is used in various industries due to its versatility and effectiveness. Understanding these applications shows the value of investing in Clemco products.
Construction
In construction, Clemco blasting equipment prepares surfaces for painting or coating. It effectively removes old paint, rust, and contaminants, ensuring strong bonds between surfaces and coatings.
Automotive
Automotive professionals use Clemco sandblasters to restore vehicles, efficiently removing rust and old paint. This process improves aesthetics and prolongs vehicle life. A local auto body shop reported a 30% reduction in time spent on rust removal after switching to Clemco equipment.
Manufacturing
In manufacturing, sandblasting prepares parts before coating or assembly. Clemco’s precision equipment ensures proper surface preparation, leading to higher quality products.
Marine
The marine industry benefits from Clemco equipment for cleaning boats and ships. Sandblasting removes marine growth, old paint, and rust, helping maintain vessel integrity and appearance.
Industry | Application | Benefits of Clemco Sandblasting Equipment |
Construction | Surface preparation for painting or coating | Efficient removal of contaminants, leading to strong bonding with coatings |
Automotive | Vehicle restoration | Reduces time spent on rust removal, enhances aesthetics and longevity |
Manufacturing | Prepares parts before coating or assembly | Ensures high-quality surface preparation for better final products |
Marine | Cleaning boats and ships | Removes marine growth and rust, maintaining integrity and appearance of vessels |
Featured client/products:
Glass Floors | Semi Truck Ramp | Glass Blocks| SEO Services Near Me | Steel Yard Ramp | Ramp for Loading Dock | Glass Flooring | Loading Dock Ramps | Portable Yard Ramp | SEO Company Near Me | SEO Agency Akron | SEO Expert Near Me | Marketing Agencies Near Me | Marketing Agency Akron
Yard Ramps | Yard Ramp