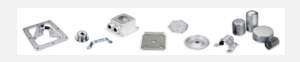
The Various Methods of Deep Draw Stamping
There’s no limit to the number of industries and applications a custom metal component could be expected to fit into. Experts rely on different methods for shaping and producing these special products in order to get the quality and specifications they need.
So what exactly is deep draw stamping? Deep draw metal stamping is a unique approach to sheet metal forming that involves drawing flat sheet metal into a die in a circular motion, to create a variety of metal components. The name “deep draw” refers to the components involved, which are generally wider and have more depth.
These depths are created by redrawing the component through a series of dies, which reduces the width even further while increasing length. It’s common for components to be deep draw partially to create various diameters throughout the part. This process reduces costs in comparison to turned parts, which need more materials.
The tool and die industry relies on deep draw components manufacturers to help them create various shapes for the automotive, aerospace, and electrical appliance industries. With so many unique components and custom applications, several methods need to be applied to create the right product.
Let’s take a look at some of these deep draw stamping methods.
#1: Deep Draw Stamping with Beading and Threading
Beads often help to reduce material consumption in drawing operations. A step bead, or offset bead, forces the metal to bend and unbend before the metal enters the draw die cavity. The main advantage of using step beads is the reduced material consumption they offer.
Conventional half-round beads are typically placed farther away from the deep draw stamping cavity than step beads. This is because the draw bead portion can become thin and weak if it is placed close to the draw punch cavity. This weak area can break during production and result in die damage. To prevent metal from pulling off the draw beads during the deep drawing process, more metal is used to obtain the finished part geometry.
When long, thin components are needed, forming threads into the component with a wheel and arbor is an easy task thanks to deep draw metal stamping. Everything from the widest to the thinnest diameter is made possible.
#2: Piercing Processes for Deep Draw Stamping
Bottom piercing is a method that refers to cutting a round or shaped section of metal out from the drawn component. The ability to puncture creates more shaping opportunities for the tool and die industry and partners with coining, which includes displacing the metal for shape formation in the component.
Side piercing places holes in the sidewall of the drawn component and allows for shape-changing depending on the deep draw component’s specifications. The possibilities with piercing are customizable when you work with the right deep draw metal stamping professionals.
#3: Deep Draw Metal Stamping with The Curling Method
Curling allows for metal to be rolled under a curling die to form a rolled edge on the component. This is perfect for creating a beveled edge. Once a pilot hole is created, a punch with a large diameter pushes through and causes the metal to increase in length.
#4: Deep Draw Stamping Methods for Reducing Material
When you need a component with a more customized thinner wall, there are plenty of options available from trusted deep draw metal stamping manufacturers. Ironing is the thinning the walls of the components, and necking refers to reducing a section of the component to a smaller diameter than the rest of the part. Being able to adjust the diameter of your metal stamping components walls allows for even further customization.
Deep draw stamping manufacturers also need to be able cut away metal that is necessary for drawing the part from the finished component. This ability to trim is instrumental in deep draw stamping.
#5: Deep Draw Stamping | Notches and Rib Forming
Creating inward protrusions is another common need in deep draw stamping. The process of notching involves cutting a notch. For creating an outward or inward protruding rib on the part, the appropriately named process of rib forming fills this exact need.
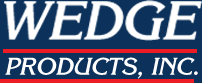
Who are Deep Draw Stamping Metal Manufacturers I Can Trust? | Wedge Products
Companies world wide have been relying on Wedge Products to create high-quality products with on-time delivery and competitive pricing since 1933. They offer a full range of metal stamping services, so they can fulfill the requirements of almost any application. Their state-of-the-art, 110,000 square foot facility offers efficient, precision metal and plastic stamping with a variety of materials and thicknesses.
With their experience in this unique industry, Wedge has established itself as one of the leading deep draw metal stamping manufacturers. Customer satisfaction is also a central goal of Wedge Products, so the management team works tirelessly to fulfill the needs of all customers. You can rely on Wedge to get you the components you need with exceptional quality and performance standards. Visit Wedge at https://www.wedgeproducts.com/index.html to learn more.
Featured client/products:
Glass Floors | Semi Truck Ramp | Glass Blocks| SEO Services Near Me | Steel Yard Ramp | Ramp for Loading Dock | Glass Flooring | Loading Dock Ramps | Portable Yard Ramp | SEO Company Near Me | SEO Agency Akron | SEO Expert Near Me | Marketing Agencies Near Me | Marketing Agency Akron
Yard Ramps | Yard Ramp